At MP Innovations, one of our main sources of casting business is converting fabrications to castings. Unfortunately, many part manufacturers simply don’t know about the benefits of castings or they think fabrication is more cost effective. We’ve outlined the advantages of fab to cast, along with a case study to demonstrate the impact it can have on a manufacturer’s bottom line.
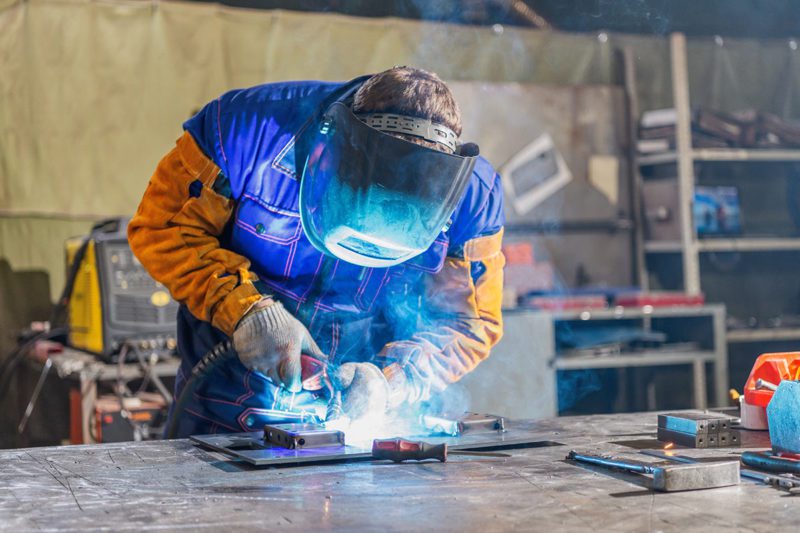
Welding can take hours to produce a single part
often including multiple steps.
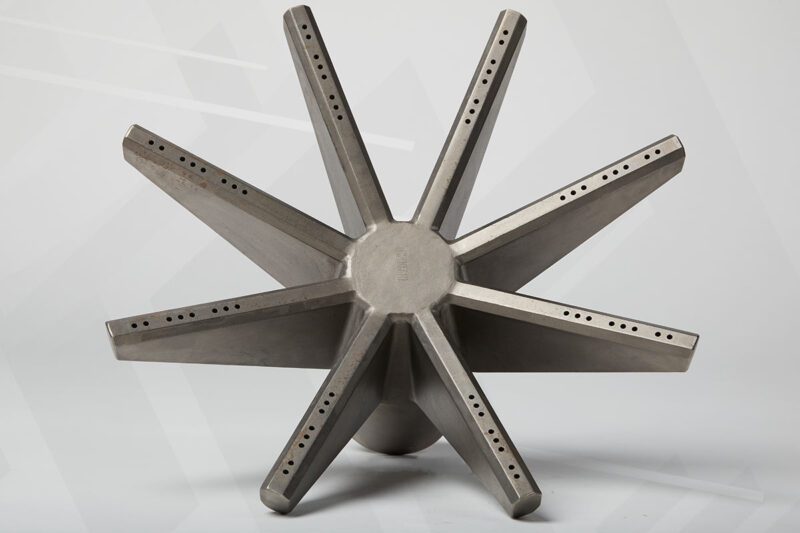
Casting can save time and money, while being more consistent.
What is Fab to Cast?
As the name implies, fabrication to casting is when a manufacturer changes a part’s production method from fabrication to casting. A labor-intensive fabrication process that may involve multiple steps, people and machines is replaced with the single step of creating investment castings from a mold. Fab to cast is a common practice that provides substantial benefits for the manufacturer, ranging from cost savings to improved aesthetics.
Benefits of Fabrication to Casting
Cost Reduction
Investment castings are more cost effective than fabrications.
Lower Manpower Needs
Casting delivers a finished product, whereas fabrication may require multiple steps and possibly even finishing parts in-house.
Reduced Welding Requirements
Investment castings can meet tight tolerances, often reducing or eliminating need for machining.
Improved Part Consistency
Fewer variables in the casting process results in more consistent parts.
Increased Part Strength
Precise design plus elimination of weld points contribute to overall stronger parts.
Better Overall Cosmetics
Investment castings allow for curved edges, a smooth finish and unique, one-piece designs that can proudly display company names.
Fab to Cast Case Study
Opportunity
While touring a customer’s facility, representatives from MP Innovations noticed a back-up of work on a part that required a tremendous amount of welding. Our team believed this would be a perfect candidate for fabrication to casting.
Solution
MP Innovations presented a proposal detailing the process of designing and producing a casting in place of the fabricated part. This process change could help clear the backlog of work and reduce the time and manpower needed to produce the part while improving consistency. By lowering the amount of welding required, there would also be little or need for machining, which adds to the cost savings of the fab to cast conversion.
Results
The overall result for this customer was better parts at lower costs. MP Innovations was able to produce a less expensive, stronger and better-looking part with faster, more consistent lead times.
Initial demand was 1200-1400 parts per year, and the casting conversion saved the client over $75.00 per part. Not only did this result in higher profit margins for the customer, but cosmetic and structural improvements to the part also increased its resale value.
Will Fab to Cast Work for Me?
Whether fab to cast is right for you depends on a number of factors. It’s worth the time to contact MP Innovations and request a free evaluation to see if your part is a good candidate for the transition.
